Why In-line Measurement?
Increase Quality. Reduce Waste.
Increase Quality. Reduce Waste.
Reliable and rapid in-line viscosity measurement is a vital tool for continuous product control. The purpose is to eliminate sampling with its potential for errors.
Unlike periodic sampling, continuous monitoring provides instant feedback of product changes so the process can be optimised in real-time.
This drives up product consistency and quality whilst minimising waste.
From Lab to Line
Viscometers were traditionally lab devices that relied on fluid samples. Attempts to replicate lab-based technology in the on-line setting have generally resulted in high-maintenance devices that struggle to match the performance of their laboratory counterparts.
The situation is now reversed. Hydramotion resonant viscosity sensors are among the smartest and toughest analysers on the plant, outperforming viscometers in the lab whilst remaining completely at ease in the process.
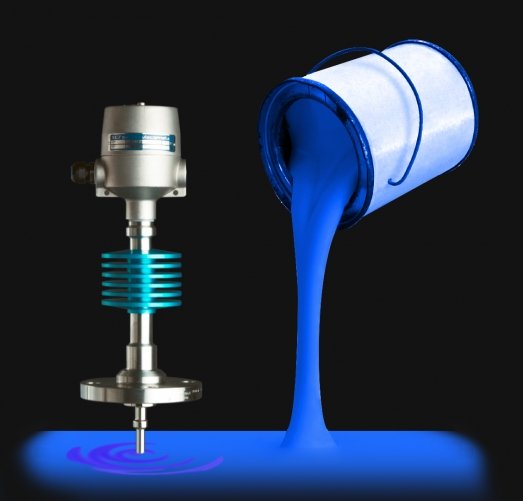
Resonance Beats All Else
Hydramotion pioneered modern resonator design to overcome the limitations of traditional methods and earlier vibrational probes. Our devices are ‘surface loaded’ so all the action takes place at the sensor. Which means they are not affected by pipe or tank sizes, flow, or any of the things that limit other techniques. They are also sensitive and extremely strong so there are no guards needed to ‘protect’ the sensor from the process.
This brings huge benefits: high accuracy, robustness and virtually no maintenance. We have driven resonator technology to the point where on-line viscosity is an attractive and affordable option for all industries.
Users are able to rely on the Hydramotion viscometer as a key control element in their process leading to full process automation with major quality and productivity benefits.
THE HYDRAMOTION DIFFERENCE
GOOD VIBRATIONS
It’s not difficult to make something vibrate in a fluid. And it’s not a very big next step to link the damping of the vibration to fluid viscosity. But measuring viscosity at the highest precision, in any vessel and in all conditions, needs a more advanced level of design and engineering science.
Resonant, or vibrational viscometers work by creating waves within the liquid being measured. There are many types of waves that can propagate in a liquid and the sort of wave used in viscometry is important.
Viscosity is a shear measurement. It can only be truly assessed under shear conditions, so we use shear waves. Other types of vibrational waves are avoided as they can behave unpredictably in process environments.
To the naked eye, nothing moves. The solid stainless steel sensor element is submerged in the fluid and made to move back and forth microscopically at a specific frequency. This is “resonance”. As the surface of the sensor shears through the liquid, energy is lost to the fluid due to its viscosity.
The dissipated energy is accurately measured by microprocessor-controlled electronics and then equated back to viscosity. Higher viscosity causes a greater loss of energy and hence a higher reading.
Hydramotion’s continuous investment in research and development keeps us at the forefront of the in-line viscosity field. This ensures our viscometers set the highest standards of performance and also deliver the maximum user experience.
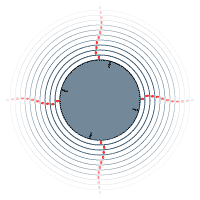

The harnessing of the wave dissipation principle with solid engineering design gives Hydramotion the combination of incredible sensitivity and toughness.
No To
Everything
NO ROUTINE MAINTENANCE
NO GAPS OR CREVICES
NO SEALS OR BEARINGS
NO FLUID TRAPS
NO RANGE CHANGES
The more work you have to do once you own a viscometer, the more costly it becomes in terms of time and money. That’s why we’ve eliminated all the things that require your intervention so there are no hidden costs of ownership and you get the maximum benefit from the instrument.
NO MOVING PARTS
NO GUARDS OR SHROUDS
NO VUNERABLE PARTS
NO FREE ELEMENTS
NO RECESS MOUNTING
All Hydramotion viscometers are built to last. Simultaneously sturdy and fluid-sensitive, there is a choice of materials and finishes to ensure long duty in the harshest environments.
NO ON-SITE RECALIBRATION
NO INSTALLATION DEPENDENCE
NO GAP DEPENDENCY
NO GAS BUBBLE INTERFERENCE
NO FLOWRATE EFFECTS
Product calibration is a major part of the manufacturing process. That calibration is preserved regardless of installation, flow, bubbles or solids. This means there are no ‘adjustments’. So you can locate, or relocate your viscometer anywhere without compromising accuracy.
NO ORIENTATION REQUIREMENT
NO SPECIAL MOUNTING
NO LIMIT ON PROCESS FITTING
We keep costs and inconvenience low by ensuring the viscometer is ready for use out of the box wherever you put it. Choose any fitting, in any orientation, in the location that suits your application. We have a Special Ops division to handle anything out of the ordinary.