Many process plants are still missing their biggest opportunity to improve reaction control.
Process control is critical. It can be the difference between an on-spec batch and a costly failure. But in many plants, real control is still limited by manual sampling and offline measurement. It’s not just the time it takes. It’s the lag between information and action.
In a high-stakes polymerisation process, 30 minutes without visibility is both inefficient and expensive. But that’s the reality of relying on manual processes and educated guesswork.
We give you real-time viscosity measurements to determine reaction endpoint.
Control polymerisation with precision. As polymer chains grow, viscosity rises – a direct indicator of reaction progress. Hydramotion’s inline viscometers give you instant insight into reaction progress, so you can hit the endpoint exactly when it matters.
![]() Reduce WasteEliminate manual sampling errors, and avoid missed endpoints that lead to costly over-or-under processing failures. |
![]() Increase QualityEnable reactions to be terminated at the optimal point, optimising product quality and reducing batch inconsistencies. |
![]() Improve ProductivityReduce lag from lab results, shorten batch times, and enhance throughput. Run more batches per day with reduced energy consumption. |
Trusted By
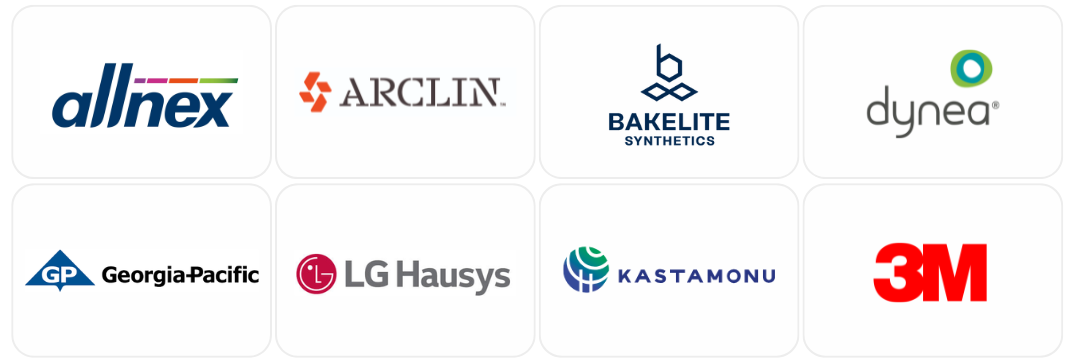
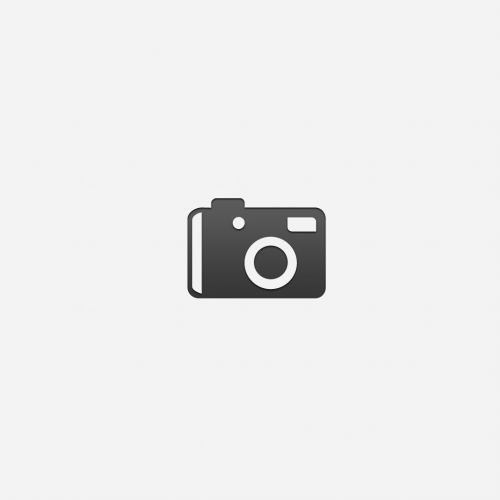.png?)
OPTIMISE EVERY REACTION
MAXIMISE EVERY BATCH
Hydramotion XL7 viscometers provide precise, real-time monitoring of viscosity changes throughout polymerisation or depolymerisation, enabling complete reaction control.
The robust stainless-steel sensor sits in the heart of the reaction and captures these changes moment-by-moment, ensuring you know exactly when the endpoint is reached.
This eliminates the need for manual sampling, saves wasted energy, and helps you achieve consistent, high-quality results across every batch.
We’ve got you covered
The XL Series has become the global standard for reaction control. These are true in-line workhorses designed for continuous use without intervention in extremes of temperature, pressure, flow and viscosity range. High accuracy and repeatability is rigorously maintained regardless of process conditions or plant noise.XL7’s are configurable for almost every possible installation with virtually any process fitting. All viscometers carry IS Safety Certifications and are provided in a range of optional materials including; Alloy C22, C276, 2507 and more.
Reactor Installations
Engineered Solutions
BUILT FOR ANY TANK
Install in any orientation. In a tank or vessel of any size. All that is required is a suitable mating process fitting. And where there’s limited availability, we will design something custom to fit.
Our special ops division routinely deals with many complex design objectives. Working with your existing plant layout, our engineers use their knowledge and expertise to create a perfect fit – anything from a slight alteration to an extension of several metres. We have a huge legacy of experience to draw on and can cope with just about anything.
“The Hydramotion viscometer is the largest single improvement we have made in the manufacturing process and it continues to help us keep our products within specification and reduce waste.”
“a truly ‘fit-and-forget’ instrument that enabled us to remove some of the ‘art’ from polymerisation and replace it with science.”
Zetachem (Division of Omnia Group)
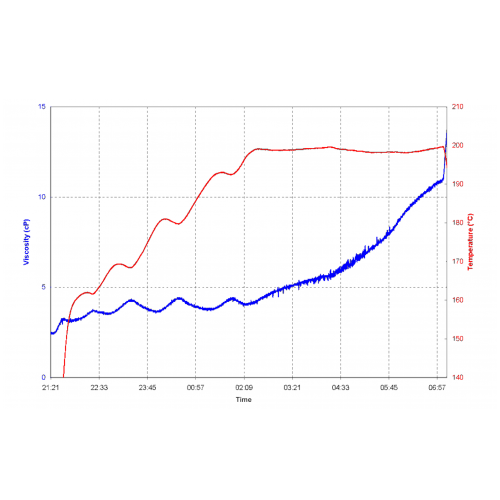
Application Note
XL7 Eliminates Batch Failures Through Endpoint Detection
Hydramotion’s custom XL7 viscometer, built to handle demanding formaldehyde resin processes, provides a precise solution for identifying reaction endpoints.
By allowing operators to monitor viscosity in real-time, the XL7 ensures accurate quenching at just the right moment, eliminating batch failures and driving down production costs.
Application Note
Streamlining PET Flake Recycling with In-Tank Viscosity Monitoring
A PET recycling facility struggled with energy efficiency and consistency in their glycolysis depolymerisation process because of variability in post-consumer recyclable materials.
After installing the XL7-HT they were able to observe the variability in real time and adjust the process conditions accordingly. Batch processing time was also reduced by up to 2 hours, resulting in significantly lower energy consumption. The time saved meant the facility could run more batches per day whilst also achieving a greater batch-to-batch consistency.
Read the application note>
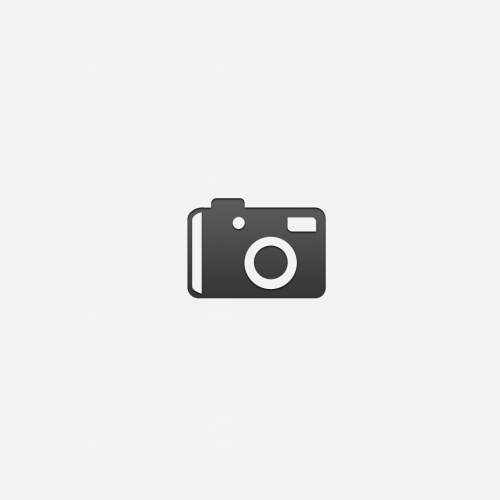.png?x=-0.84375&y=-0.46875&w=504&o=500?)
XL7 KEY FEATURES
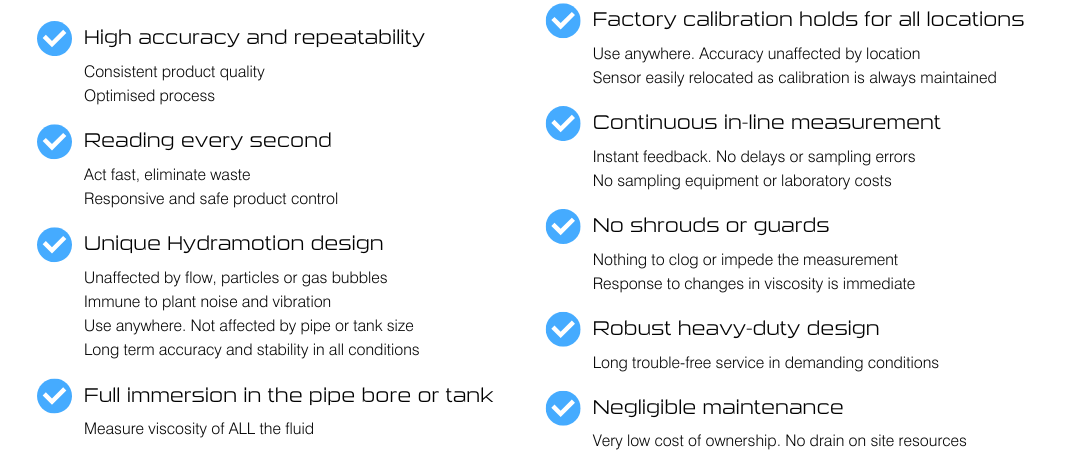
Ready to learn more?
If you’re facing inconsistent product quality, high batch failure rates, excessive energy consumption, or concerns about manual sampling, Hydramotion’s inline viscometers may be the ideal solution:- Real-time tracking of reaction progress for precise endpoint detection
- Measure viscosity with high accuracy and repeatability, regardless of process conditions
- Eliminate time delays and human error associated with manual sampling
- Cut production costs by preventing over-runs, improving consistency and reducing failure rates